Finite element modelling and simulation
The use of modern calculation and simulation software in the concept and development phases of new products significantly contributes to shortening development times, improving product parameters such as weight & material savings, increasing stiffness and minimising natural vibrations. Additional positive effects include the identification of weak points and the associated reduction of product risks and damage prevention.
A precondition for successful optimisation through FEM modelling and simulation is the software itself and very powerful computing technology. But above all, it is the many years of experience in the approach and implementation in the modelling and the analysis of the simulation results.
Based on experience from numerous research and customer projects we offer the following services.
Service offering
- magnetic field simulation:
- design and layout of product-specific magnetic actuators, such as direct drives, voice coils, magnetic bearings, and others
- design of magnetic shielding
- coupled thermal analysis
- dynamic analysis
- dynamic simulation
- modal analysis: determination of natural frequencies and vibration modes of components
- harmonic & transient analysis: determination of transfer functions between machine parts
- temperature simulation
- thermally induced temperature distribution
- optimisation of cooling systems
- thermally induced deformation e.g. for mechanics and electronics
- strength and deformation: linear and non-linear calculations and standard-compliant verification
- fluidics simulation: simulation of the flow behaviour of fluids in (micro-) channels and chambers
- MEMS simulation: simulation of the behaviour of MEMS structures, such as membranes and comb structures
Contact
Contact
Dr.-Ing. Ludwig Herzog
Head of Mechatronics
ludwig.herzog(at)imms.de+49 (0) 3677 874 93 60
Dr. Ludwig Herzog will provide detail on our research on magnetic 6D direct drives with nm precision for the nm measurement and structuring of objects. He supports you with services for the development of mechatronic systems, for simulation, design and test of MEMS as well as for finite element modelling (FEM) and simulation.
Related content
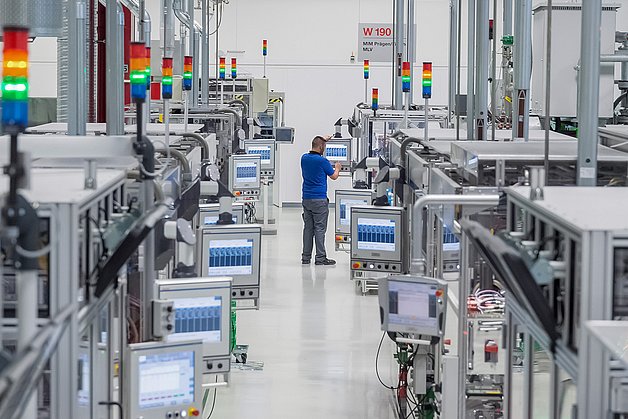
Project
RoMulus
Systematic design and economical manufacture for intelligent multi-sensor systems in small quantities
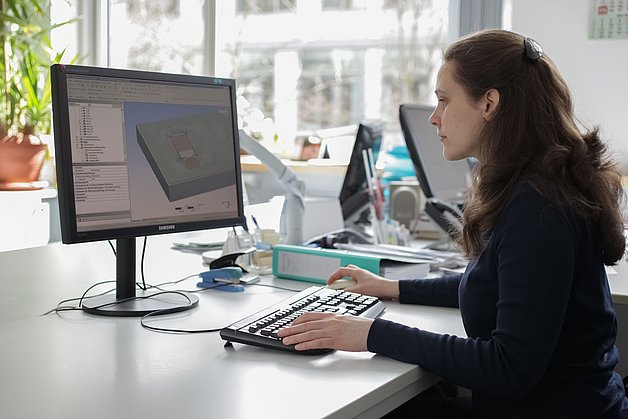
Project
MUSIK
IMMS has investigated, modelled and validated MEMS characteristics to develop basic blocks for a universally applicable method for MEMS design.
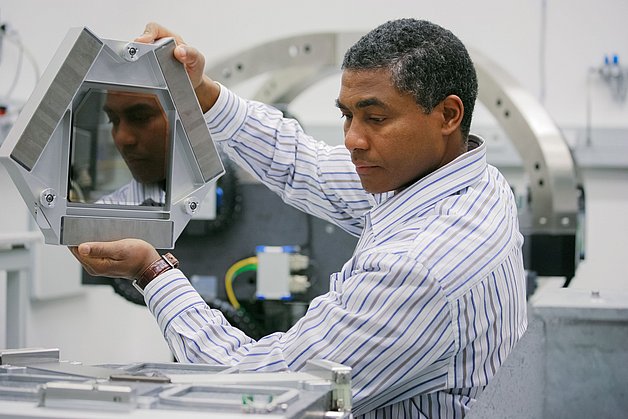
Project
Mag6D
Within the project a novel planar drive system was developed which is magnetically guided and moves objects with nanometer precision.
Operation and performance evaluation of vertical nanopositioners for 10 mm stroke in a 3D lift and tilt test setup
Steffen Hesse1. Michael Katzschmann1. Alex S. Huaman1. Stephan Gorges1. Eberhard Manske2.euspen – Special Interest Group Meeting: Precision Motion Systems & Control, 15th – 16th November 2022, s-Hertogenbosch, The Netherlands, NL
1IMMS Institut für Mikroelektronik- und Mechatronik-Systeme gemeinnützige GmbH, 98693 Ilmenau, Germany. 2Institut für Prozessmess- und Sensortechnik, Technische Universität Ilmenau, Ilmenau, Germany.Development of an Integrated Guiding and Actuation Element for High Dynamic Nanopositioning Systems
Stephan Gorges1. Bianca Leistritz1. Steffen Hesse1. I. Ortlepp2. G. Slotta3. Christoph Schäffel1.Ilmenau Scientific Colloquium 2017, Session 1.1 – Precision Measurement Technology, 11-15 September 2017, Ilmenau
1IMMS Institut für Mikroelektronik- und Mechatronik-Systeme gemeinnützige GmbH, 98693 Ilmenau, Germany. 2Institut für Prozessmess- und Sensortechnik, TU Ilmenau. 3AeroLas GmbH.A contribution towards model-based design of application-specific MEMS
Jenny Klaus1. Eric Schäfer1. Roman Paris1. Astrid Frank1. Ralf Sommer1.In Integration, the VLSI Journal, Volume 58, 2017, Pages 454-462, ISSN 0167-9260, DOI: doi.org/10.1016/j.vlsi.2017.03.014
1IMMS Institut für Mikroelektronik- und Mechatronik-Systeme gemeinnützige GmbH, 98693 Ilmenau, Germany.Investigations of metal systems in a silicon ceramic composite substrate for electrical and thermal contacts as well as associated mounting aspects
M. Fischer1. T. Welker1. B. Leistritz2. S. Gropp1. C. Schäffel2. M. Hoffmann1. J. Müller1.Ceramic Interconnect and Ceramic Microsystems Technologies, Additional Conferences (Device Packaging, HiTEC, HiTEN, & CICMT): May 2016, Vol. 2016, No. CICMT, pp. 000107-000110, DOI: dx.doi.org/10.4071/2016CICMT-WA22
1Technische Universität Ilmenau, IMN MacroNano®, Ilmenau, Germany. 2IMMS Institut für Mikroelektronik- und Mechatronik-Systeme gemeinnützige GmbH, D-98693 Ilmenau, Germany.