Project NanoFab
IMMS has been working on solutions for a highly dynamic drive system for multi-axis manufacturing and processing of objects with nanometre precision in the Research Training Group 2182 ”NanoFab“.
PhD students have been working in the NanoFab Research Training Group (RTG) 2182 on a project funded by the DFG (German Research Council). The work is on tip-based and laser-based three-dimensional nanofabrication techniques applied to large (macroscopic) areas. The supervisors of the PhD students are teaching and research staff of Ilmenau TU and IMMS under the leadership of the Institute of Process Measurement and Sensor Technology which is concerned with sensors and process measurements in manufacturing in the Mechanical Engineering Faculty.
Nanofabrication – not used up to now for large objects and still without error correction
The RTG is investigating techniques of manufacturing that will in future enable macroscopic objects to be made to the nanometre scale of precision in ever more fields of manufacture. Admittedly, it is already possible to produce structures below ten nanometres using nanofabrication, but an object area of only a few hundred square micrometres is the limit, and speeds are slow and accuracy limited. The particular challenge being taken up by the NanoFab RTG is that error correction should be able to take place even while the nanofabrication is running; to date, straight measurements have been possible, but in-process correction has not. Currently, if static or dynamic deviations of position arise during nanoproduction, among the problems they cause, are errors in the geometry, irregularities in shape or roughness in the structures or objects – all of which can be established only with hindsight.
There are six investigative subprojects, with the NanoFab TSG working on a variety of fronts in around the practicability of freeforms manufactured in 3D at nanometre precision and with in-process error correction. The fronts include theory and metrology, tools and parallelisation, kinematics and control: control is relevant in lithography, optical microsystems, real-time process management and multi-dimensional drive and positioning dynamics.
IMMS at work on highly dynamic nanofabrication drives
At the Institute, a drive system is being explored that permits multi-axis manufacturing and processing of objects with nanometre accuracy. In such a drive, extremely even and smooth movement must take place in the complex spatial trajectories dictated by the geometry of what is to be fabricated.
To achieve high machining speeds, the entire drive system (actuators, guides, sensors, amplifiers, control) must be able to execute the set points with minimal deviation and extremely fast. It will be necessary to develop drive systems with near-perfect reproducibility and synchronism if multi-axial nanofabrication of relatively large objects is to be achieved. 3D-positioning of objects is already possible; further degrees of movement are necessary, actuators and sensors need to be integrated into the drive structure and controls.
The research emphasis is on synchronicity in the movements, temperature maintenance, minimal power dissipation and minimisation of drive and disturbance forces. In these innovative drives for nanofabrication, what is crucial is highly dynamic drive and positioning capable of being adapted to the motion required, so that the consequences for drive, controls and overall dimensioning must all be taken into account.
Acronym / Name:
NanoFab / Tip-based and laser-based three-dimensional nanofabrication techniques applied to large (macroscopic) areasDuration:2017 – 2026
Project website:graduate college NanoFab
Application:
Research institutions and ultra-precision mechanical engineering|Precision machining of freeform surfaces e.g. precision optics| Fabrication of aspheresResearch field:Magnetic 6D-direct drives with nanometre precision
Related content
A virtual metrology frame test setup using fiber interferometric sensors
Davi Anders Brasil1. Steffen Hesse1. Ludwig Herzog1. Thomas Fröhlich2. Thomas Kissinger2.22nd International Metrology Congress (CIM 2025), Lyon, France, March 11-14, 2025
1IMMS Institut für Mikroelektronik- und Mechatronik-Systeme gemeinnützige GmbH, Ehrenbergstraße 27, 98693 Ilmenau, Germany. 2Institute of Process Measurement and Sensor Technology, Technische Universität Ilmenau.Investigation of distance measurement reproducibility for a long-range nanopositioning machine combined with a laser focus sensor
Davi Anders Brasil1. Steffen Hesse1. Michael Katzschmann1. Ludwig Herzog1. Thomas Fröhlich2. Thomas Kissinger2.20th International Conference on Precision Engineering (ICPE2024), Sendai, Japan, October 23-26, 2024
1IMMS Institut für Mikroelektronik- und Mechatronik-Systeme gemeinnützige GmbH, Ehrenbergstraße 27, 98693 Ilmenau, Germany. 2Institute of Process Measurement and Sensor Technology, Technische Universität Ilmenau, Ilmenau, Germany.Investigations on tip-based large area nanofabrication and nanometrology using a planar nanopositioning machine (NFM-100)
Jaqueline Stauffenberg1. Johannes Belkner1. Denis Dontsov2. Ludwig Herzog3. Steffen Hesse3. Ivo W Rangelow1,4. Ingo Ortlepp1. Thomas Kissinger1. Eberhard Manske1.2024 Meas. Sci. Technol. 35 085011, DOI: doi.org/10.1088/1361-6501/ad4668
1Institute for Process Measurement and Sensor Technology, Department for Mechanical Engineering, Gustav-Kirchhoff-Straße 1, Ilmenau, Germany. 2SIOS Meßtechnik GmbH, Am Vogelherd 46, 98693 Ilmenau, Germany. 3IMMS Institut für Mikroelektronik- und Mechatronik-Systeme gemeinnützige GmbH, Ehrenbergstraße 27, 98693 Ilmenau, Germany. 4nano analytik GmbH, Ehrenbergstraße 1, 98693 Ilmenau, Germany.Unconventional, lateral measurements with laser focus sensors for nanopositioning stages
Davi Anders Brasil1. Michael Katzschmann1. Steffen Hesse1. Ludwig Herzog1. T. Fröhlich2. T. Kissinger2.euspen Special Interest Group Meeting, "Micro/Nano Manufacturing", 28. - 29. November 2023, Ilmenau, Germany
1IMMS Institut für Mikroelektronik- und Mechatronik-Systeme gemeinnützige GmbH, Ehrenbergstraße 27, 98693 Ilmenau, Germany. 2Institute of Process Measurement and Sensor Technology, Technische Universität Ilmenau, Germany.
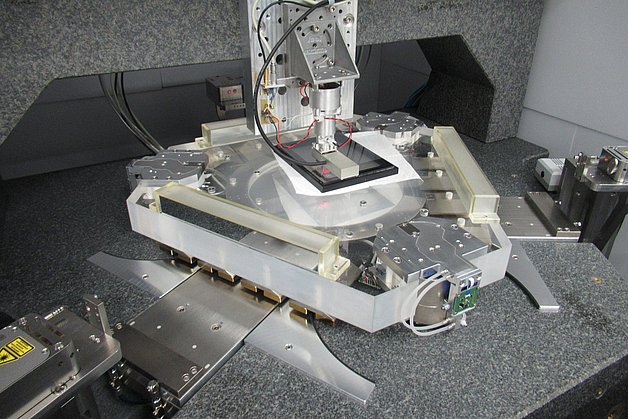
Event,
euspen SIG: Micro/Nano Manufacturing 2023
euspen Special Interest Group Meeting: Micro/Nano Manufacturing 2023
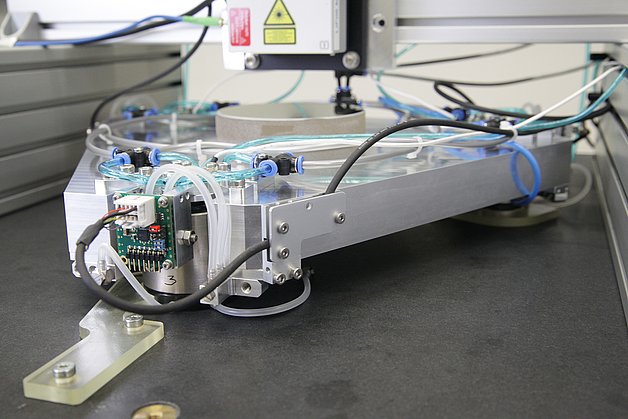
Event,
euspen 2022
Euspen Special Interest Group Meeting: Precision Motion Systems & Control 15th – 16th November 2022
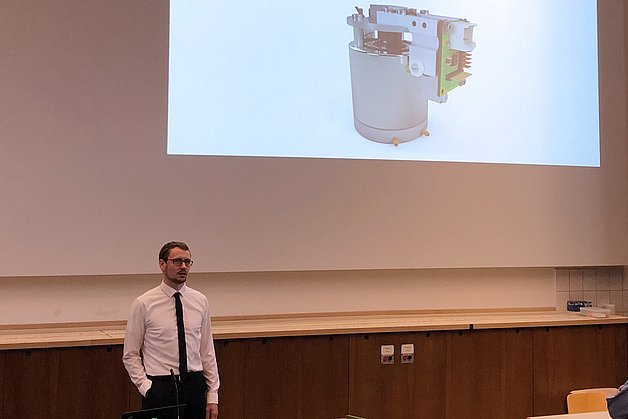
Press release,
Ready for Take-off – Vertikalantrieb für die 3D-Nanofertigung vorgestellt
IMMS-Doktorand verteidigt Promotion im DFG-Graduiertenkolleg NanoFab
Contact
Contact
Dr.-Ing. Ludwig Herzog
Head of Mechatronics
ludwig.herzog(at)imms.de+49 (0) 3677 874 93 60
Dr. Ludwig Herzog will provide detail on our research on magnetic 6D direct drives with nm precision for the nm measurement and structuring of objects. He supports you with services for the development of mechatronic systems, for simulation, design and test of MEMS as well as for finite element modelling (FEM) and simulation.
Funding
The Research Training Group 2182 on Tip- and laser-based 3D-Nanofabrication in extended macroscopic working areas (NanoFab) is funded by the German Research Foundation (DFG) under the funding code DFG GRK 2182.