Development of mechatronic systems
We develop actuator systems and open- and closed-loop controls as embedded solutions according to customer specifications with highest demands on precision, dynamics, available space, performance and efficiency. A model-based system design approach allows us to find the best possible solution for your product. With the help of powerful simulation and rapid prototyping tools, we develop solutions for a fast and flexible initial commissioning of your system. We create prototypes and support you from the idea to the start of series production. Based on experiences from numerous research and customer projects we offer the following services.
Service offering
- concept and feasibility studies in the field of magnetic drives
- exact calculation and design of electromagnetic drive systems as integrated components
- high-precision electromagnetic direct drives up to 6D
- magnetic guides and bearings
- design of open-loop and closed-loop controls and implementation on customer hardware
- virtual prototypes
- production transition
Our portfolio includes:
- exact calculation and design of electromagnetic drive systems as integrated components
- systematic use of FEM for the modelling of:
- statics, structural dynamics,
- magnetics, electrostatics,
- thermal and coupled phenomena,
- to eliminate costly redesigns and increase reliability and robustness
- thermal management of actuator systems:
- thermal modelling
- temperature control concepts
- validation
- design of air/magnet guided actuator systems with nm-precision
- actuator systems for vacuum applications
- design of actuator systems for applications with highest dynamics (200 m/s2)
- model-based and experimental optimisation of machine dynamics and vibration behavior
- Developing solution concepts on the basis of a model-based overall system consideration
- Controls for actuator systems with nm precision
- Hardware/software codesign of controls for actuator and sensor systems
- Reliability and efficiency through structured development process
- Powerful control algorithms:
- adaptive,
- minimal system excitation
- disturbance compensation
- Architecture design and parameterisation with rapid prototyping tools
- implementation on target hardware
- metrological identification/verification of system dynamics/model
- real-time test of control units on HIL test benches
- wired real-time networking
- Adaptation of real-time operating systems incl. porting to highly resource-constrained HW platforms
Application fields and technical equipment
- optical inspection and analysis
- medical technology
- laser precision machining
- multi-coordinate metrology with nm and sub-nm precision
- MEMS and microsystem technology manufacturing
- nanotechnology
- open-loop and closed-loop controls for embedded direct drives (linear, rotary) e.g. in medical devices
- open-loop and closed-loop controls for 6D-positioning, nm-precision, high dynamics
- extensive design software such as MATLAB/Simulink, ANSYS, Maxwell and powerful computing technology
- interferometric and capacitive displacement and angle measurement technology
- measurement technology for magnetic quantities
- vibration and analysis measurement technology
- precise temperature control, temperature measurement, thermography
- vacuum chambers for experimental setups
- development environments for industrial control systems such as B&R, Beckhoff
- rapid prototyping systems, such as dSpace, for fast initial commissioning
Contact
Contact
Dr.-Ing. Ludwig Herzog
Head of Mechatronics
ludwig.herzog(at)imms.de+49 (0) 3677 874 93 60
Dr. Ludwig Herzog will provide detail on our research on magnetic 6D direct drives with nm precision for the nm measurement and structuring of objects. He supports you with services for the development of mechatronic systems, for simulation, design and test of MEMS as well as for finite element modelling (FEM) and simulation.
Related content
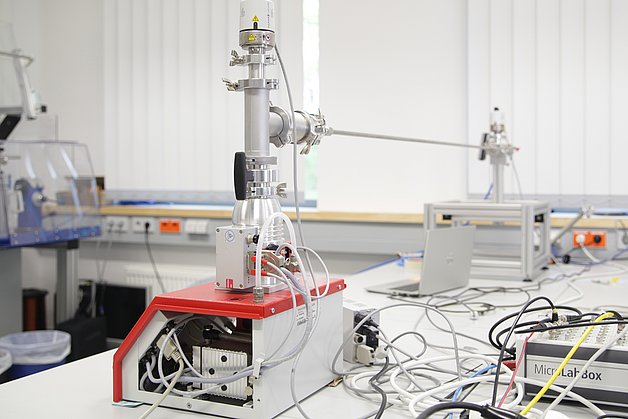
Project
OptoMed vacuum air bearings
Air bearings in high-precision vacuum applications? Together with our partners, we are exploring the technical feasibility of this (apparent) contradiction.
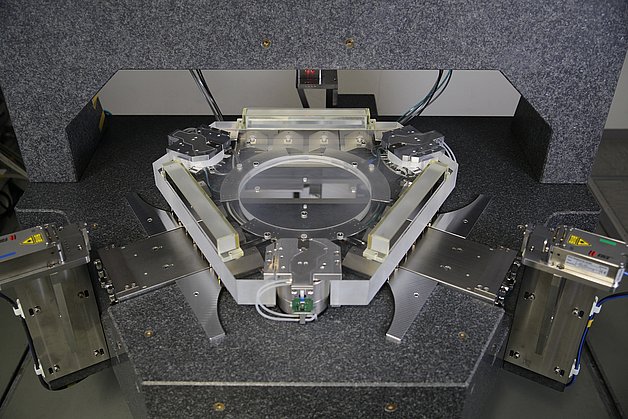
Project
K4PNP+Z
IMMS developed actuators to position objects in planes with diameters up to 200 mm and a vertical stroke of 25 mm with nanometre precision.
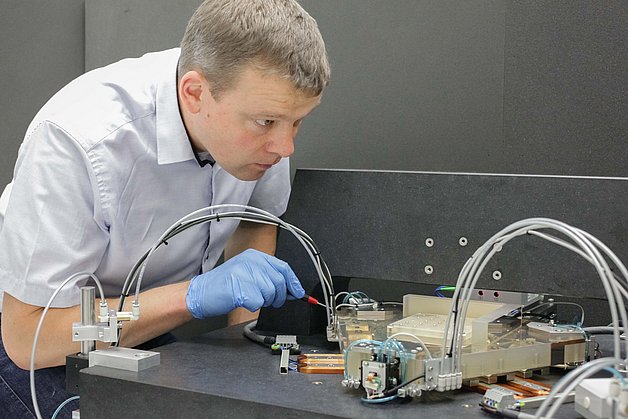
Project
INPOS
Novel 6DOF integrated direct drive moving large objects with small vertical dimensions through nanometre spaces
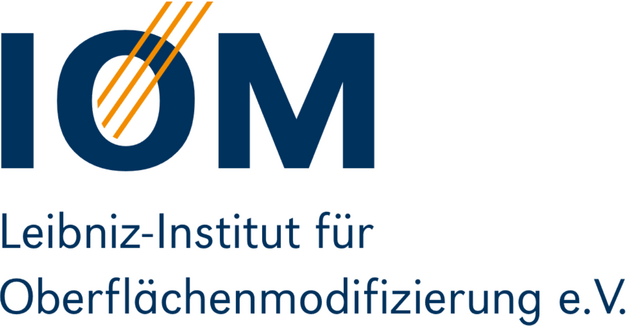
Reference
Prof. Dr. Thomas Arnold, Leibniz IOM
“We are extremely pleased with the resulting demonstration device. Besides proven competence in drive design and experience of product development in the service of research institutes, IMMS also brought to the task a highly professional, purposeful and constructive approach.”
Reference
Prof. Dr. Almuth Einspanier, Leipzig University
”Ever since 2011, we have been researching a process that will enable us reliably to determine the sex of a chicken by hormone analysis before it hatches. In IMMS we found a partner to investigate with us whether mechanised, multiple sampling might be feasible in principle.”
NPS6D100—A 6D Nanopositioning System with Sub-10 nm Performance in a Ø100 mm × 10 mm Workspace
Steffen Hesse1. Alex S. Huaman1. Micheal Katzschmann1. Ludwig Herzog1.Actuators 2025, 14, 361, DOI: doi.org/10.3390/act14080361
1IMMS Institut für Mikroelektronik- und Mechatronik-Systeme gemeinnützige GmbH, Ehrenbergstraße 27, 98693 Ilmenau, Germany.Automated Design Methodology for Electromagnetic Energy Harvesters
Bianca Leistritz1. Ludwig Herzog1.Sensors 2025, 25, 3358, DOI: doi.org/10.3390/s25113358
1IMMS Institut für Mikroelektronik- und Mechatronik-Systeme gemeinnützige GmbH, Ehrenbergstraße 27, 98693 Ilmenau, Germany.A method for dynamic interferometric characterization of air bearings for nanopositioning stages
Steffen Hesse1. Michael Katzschmann1. Alex Huaman1. Parastoo Salimitari1. Ludwig Herzog1.Ilmenauer Nacht der Interferometrie und Internationales Wissenschaftliches Symposium zum Welttag der Interferometrie, 8. - 9. April 2025, Technische Universität Ilmenau, Ilmenau
1IMMS Institut für Mikroelektronik- und Mechatronik-Systeme gemeinnützige GmbH, Ehrenbergstraße 27, 98693 Ilmenau, Germany.Disturbance rejection in periodic motion with enhanced constant velocity transitions using a tilt-mirror test setup
Alex S. Huaman1. Michael Katzschmann1. Steffen Hesse1. Ludwig Herzog1.euspen Special Interest Conference: Precision Motion Systems and Control, Brabanthallen, ’s-Hertogenbosch, The Netherlands, November 12-13, 2024
1IMMS Institut für Mikroelektronik- und Mechatronik-Systeme gemeinnützige GmbH, Ehrenbergstraße 27, 98693 Ilmenau, Germany.