Project MEMS2015
The IMMS tool automatically generates mechanical designs. MEMS can be simulated and verified as an entire system.
MEMS (micro-electro-mechanical systems) are one of the keys to innovative manufacture of plant and equipment. As such, they are an element of the Industry 4.0 strategic project. MEMS are being developed at enormous rates with quantities and revenues going into the billions worldwide. One of the aims of the MEMS2015 project was the combination and harmonisation of the design process for the mechanical and the electronic components of MEMS. A newly developed type of comprehensive design methodology can be expected to enable SMEs to compose their own individual, tailor-made solutions using a flexible MEMS and electronics construction kit so that they can capture a share of the MEMS boom.
The new systematic methodology IMMS developed was validated by a MEMS accelerometer. Furthermore, IMMS staff has developed a micro-chip for a MEMS module, integrating the knowledge it brought them into the new methodology.
MEMS Design at the press of a button – The methodology of synthesising MEMS exemplified in an accelerometer
There is a need for new procedures and tools in the field of MEMS design to enable smart, up-to-date, high-performance sensor-and-actuator systems to be developed. The tried and trusted modular principle from microelectronic design has been adopted by the Institute and transferred to mechanical systems and to MEMS. The two design procedures have been combined into a systematic start-to-finish procedure. As a result, MEMS can now be simulated and verified as an entire system, which means that errors can be recognised and remedied early.
One outcome is a special design tool that supports XM-SC, the SOI technology of X-FAB AG, by providing a sensor design system for computer-aided design of the electromechanical unidimensional sensors known as accelerometers. In future, it is hoped that small and medium-sized enterprises (SMEs) will be able to use the system to design their own MEMS without possessing much design experience. The tool works by using a mathematical algorithm developed at IMMS to compute the various design possibilities that might match the customer's requirements. The tool is, furthermore, a source of sensor models which the user can integrate into the design tools made by our research partners Coventor and Cadence. It will generate the necessary mechanical layouts for the manufacturing stage.
In validation of this new methodology and the new tool, IMMS has used the content of the new tool to design an accelerometer (acceleration sensor with high-precision signal evaluation) and then characterise it after fabrication.
In the RoMulus project, the design tool (originally for a unidimensional sensor) has been extended to 2- and 3-dimensional inertial sensors.
Readout circuit for a smart force sensor MEMS
There is a need for new procedures and tools in the field of MEMS design to enable smart, up-to-date, high-performance sensor-and-actuator systems to be developed. The tried and trusted modular principle from microelectronic design has been adopted by the Institute and transferred to mechanical systems and to MEMS. The two design procedures have been combined into a systematic start-to-finish procedure. As a result, MEMS can now be simulated and verified as an entire system, which means that errors can be recognised and remedied early.
One outcome is a special design tool that supports XM-SC, the SOI technology of X-FAB AG, by providing a sensor design system for computer-aided design of the electromechanical unidimensional sensors known as accelerometers. In future, it is hoped that small and medium-sized enterprises (SMEs) will be able to use the system to design their own MEMS without possessing much design experience. The tool works by using a mathematical algorithm developed at IMMS to compute the various design possibilities that might match the customer's requirements. The tool is, furthermore, a source of sensor models which the user can integrate into the design tools made by our research partners Coventor and Cadence. It will generate the necessary mechanical layouts for the manufacturing stage.
In validation of this new methodology and the new tool, IMMS has used the content of the new tool to design an accelerometer (acceleration sensor with high-precision signal evaluation) and then characterise it after fabrication.
Acronym / Name:
MEMS2015 / Schematic-Based Design of MEMS for Applications in Optics and RoboticsDuration:2012 – 2015
Project website:MEMS2015
Application:
Automation technology and Industry 4.0Research field:Integrated sensor systems
Related content
Reference
Prof. Dr.-Ing. Erich Barke
“The Erfurt branch of IMMS is involved in finding methods by which models can be efficiently simulated. Not only the excellent collaboration but also the publication success bring me much pleasure.”
Reference
Dr. Gisbert Hölzer, X-FAB
“For many years as we followed our ‘More-than-Moore’ roadmap, IMMS has been a support to us, acting as our most important research partner. The Institute melded together in sovereign fashion its skills in ASIC design and in micromechanics.”
Ansätze zur Entwicklung durchgängiger Entwurfsstrategien für MEMS
Jacek Nowak1. Jenny Klaus2. Dominik Karolewski2. Ralf Sommer1,2.edaWorkshop 14, Hannover, 13.-14. Mai 2014, Tagungsband, VDE-Verlag, ISBN: 978-3-8007-3620-1
1Technische Universität Ilmenau, Ilmenau. 2Institut für Mikroelektronik- und Mechatronik-Systeme gemeinnützige GmbH, Ilmenau.Using WiCkeD in MEMS Design
Volker Boos1.MunEDA User Group Meeting, München, 10.10.2013-11.10.2013
1IMMS Institut für Mikroelektronik- und Mechatronik-Systeme gemeinnützige GmbH, Ilmenau.TalkSchematic Driven MEMS Design
Ralf Sommer1.edaWorkshop, Dresden, 14.05.2013-16.05.2013
1IMMS Institut für Mikroelektronik- und Mechatronik-Systeme gemeinnützige GmbH, Ilmenau.TalkSchematic-Based Design of MEMS for Applications in Optics and Robotics
T. Maier1. D. Meisel1. Volker Boos3. Ralf Popp2.edaWorkshop, Dresden, 14.05.2013-16.05.2013
1Robert Bosch GmbH, Stuttgart. 2edacentrum GmbH, Hannover. 3IMMS Institut für Mikroelektronik- und Mechatronik-Systeme gemeinnützige GmbH, Ilmenau.Poster presentation
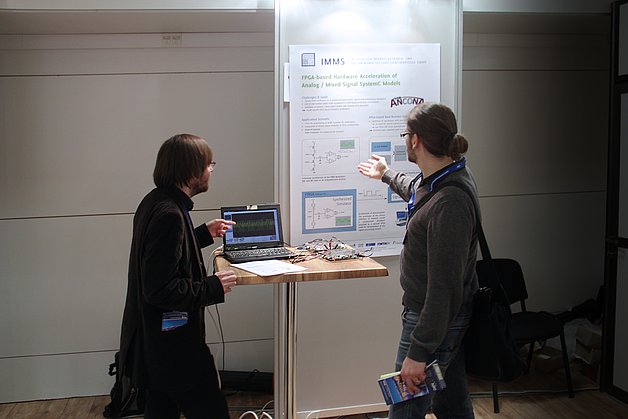
Event,
SMACD 2016
13th International Conference on Synthesis, Modeling, Analysis and Simulation Methods and Applications to Circuit Design
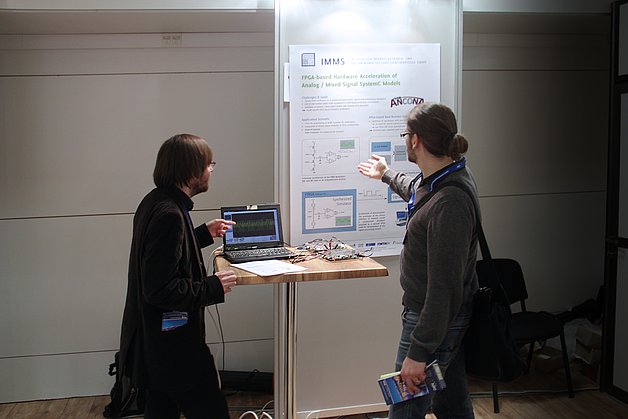
Event,
TuZ 2016
Two presentations at the 28th GMM/GI/ITG Workshop on test methods and reliability of circuits
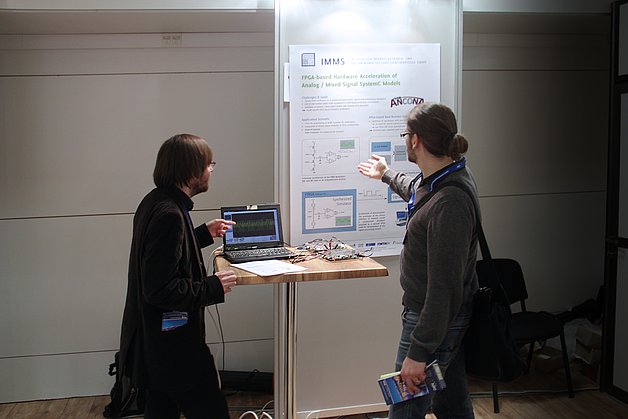
Event,
edaWorkshop 15
Lecture: "Design of Acceleration Sensors Using a Systematic MEMS-ASIC Design Flow"
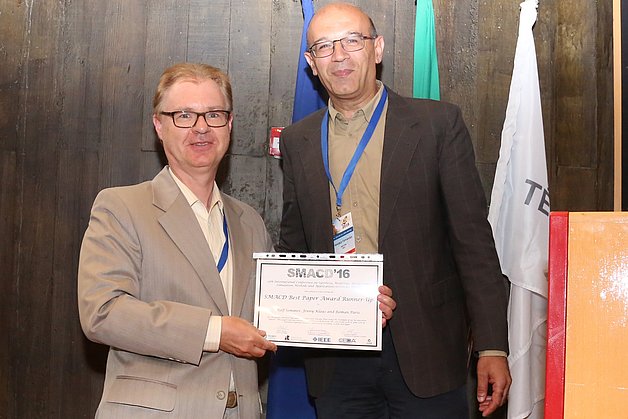
Press release,
Best Paper Award Runner-Up for MEMS-ASIC-Gesamtdesignmethodik
Implemented acceleration sensor to validate the novel method
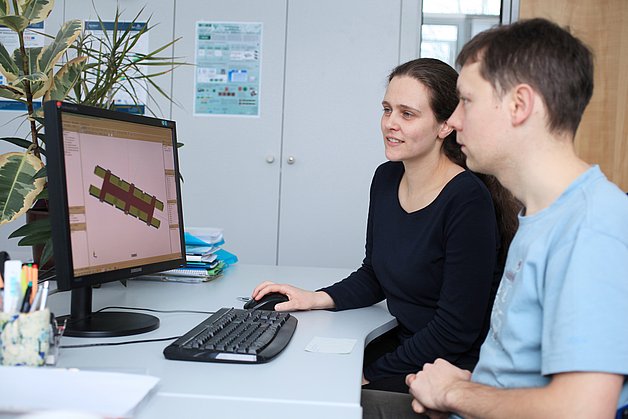
Press release,
MEMS design methodology honoured with the EDA Achievement Award 2015
IMMS and Ilmenau TU’s methodology opens up cost-efficient MEMS developments and novel applications.
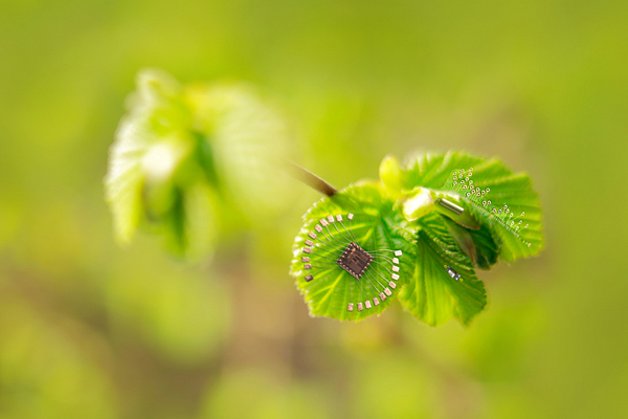
Press release,
BMBF-Projekt MEMS 2015
Contact
Contact
Eric Schäfer, M. Sc.
Head of Microelectronics / Branch Office Erfurt
eric.schaefer(at)imms.de+49 (0) 361 663 25 35
Eric Schäfer and his team research Integrated sensor systems, especially CMOS-based biosensors, ULP sensor systems and AI-based design and test automation. The results are being incorporated into research on the lead applications Sensor systems for in-vitro diagnostics and RFID sensor technology. It will assist you with services for the development of Integrated circuits and with IC design methods.
Contact
Dr.-Ing. Ludwig Herzog
Head of Mechatronics
ludwig.herzog(at)imms.de+49 (0) 3677 874 93 60
Dr. Ludwig Herzog will provide detail on our research on magnetic 6D direct drives with nm precision for the nm measurement and structuring of objects. He supports you with services for the development of mechatronic systems, for simulation, design and test of MEMS as well as for finite element modelling (FEM) and simulation.
Funding
The MEMS2015 project was funded by the BMBF (German Ministry of Education and Research) in its IKT 2020 programme, with the reference 16M3093.