CCTA 2022
Robust Tracking Control with L1 Adaptive Augmentation for a Long-Stroke Vertical Nanopositioning System: Part I
Robust Tracking Control with L1 Adaptive Augmentation for a Long-Stroke Vertical Nanopositioning System: Part II
Alex S. Huaman (IMMS) and Johann Reger (TU Ilmenau)
The authors present their work in 2 companion contributions. In both, they address the demands from semiconductor industry and other branches where high-precision drive systems for industrial plant and machinery are required to increasingly evolve towards ever more precise systems with sub-nanometre precision. At the same time, ever larger vertical movements are to be carried out in nano fabrication.
For those vertical movements of a drive system, the authors equipped an existing nanometre planar positioning system (NPPS100) with purpose-designed lifting and actuating units (LAUs). The result is a 6D system with 10 mm vertical stroke with sub-nanometre resolution.
To achieve this, each LAU was individually mounted on a test bench to perform in-depth investigations on its static and dynamic characteristics, which are instrumental in the derivation of advanced motion controllers for highest precision.
The biggest shortcoming of vertical actuation is heat emission, which produces deformations in the loads and disturbs the measurement space. In consequence, every LAU configures a complex system, comprising a pneumatic actuator to counteract the weight force while an electromagnetic drive provides the (almost zero) precision motion force, i.e. low current and consequently low heat emission.
On the one hand, emphasis is placed on an appropriate distribution criterion to handle the pneumatic and electromagnetic actuator of the vertical motion system. The proposed distribution concept proves to be effective for the ongoing application since it demands low computational costs and fulfills the (low) heat emission constraint. On the other hand, the motion controller is accomplished via a composite control law involving a nominal full-state feedback controller plus an adaptive augmentation. The nominal tracking controller fulfills the projected performance under ideal conditions and the adaptive component plays a central role for recovering the nominal reference dynamics subject to complex time-varying perturbations and external disturbances. The effectiveness and robustness of the presented control strategy is verified via real-time experiments featuring subnanometer positioning errors below 0.25 nm along the vertical travel range up to 10 mm.
Robust Tracking Control with L1 Adaptive Augmentation for a Long-Stroke Vertical Nanopositioning System: Part I
In this paper and its companion paper, we address the problem of modeling and robust adaptive tracking control for an overactuated vertical nanopositioning system. We first introduce the operation principle of the lifting modules. In relation to the integrated actuators, their dynamics and important parameters are obtained from experimental and projected data. We further derive a physical model from the relevant components of the motion system. The model is validated with measured data in order to illustrate that it adequately reflects the real behavior. Emphasis is placed on the merits of control allocation (CA) to handle the overactuated nature of the overall motion system. The proposed CA concept proves to be effective for the ongoing application since it demands low computational costs and fulfills the heat emission constraint. We close this paper with the formulation and analysis of a suitable model for the derivation of advanced control strategies.
Robust Tracking Control with L1 Adaptive Augmentation for a Long-Stroke Vertical Nanopositioning System: Part II.
In this paper and its companion paper, we address the problem of modeling and robust adaptive tracking control for an overactuated vertical nanopositioning system. In virtue of the derived model, the control is accomplished via a composite control law involving a nominal full-state feedback controller plus an L1 adaptive augmentation. To preserve PID-type robustness properties, the nominal (or baseline) controller comprises integral action and features sufficiently high bandwidth for mere stabilization and attenuation of slowly varying disturbances. The L1 adaptive component plays a central role for recovering the nominal closed-loop dynamics in the presence of complex time-varying perturbations and external disturbances. The effectiveness and robustness of the presented control strategy is verified via real-time experiments featuring subnanometer positioning errors which seem to be fully-dominated by the measurement noise.
Related content
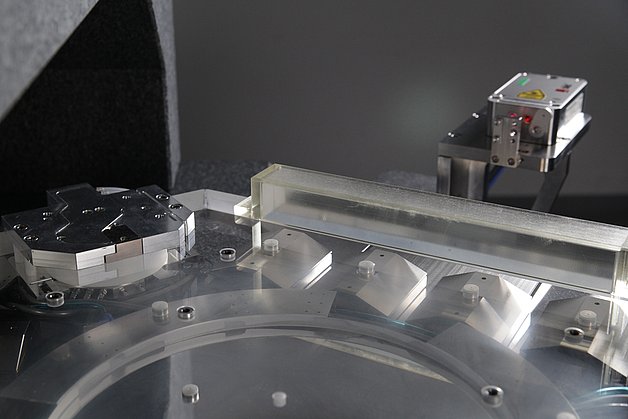
Project
NanoFab
IMMS has been working on solutions for a highly dynamic drive system for multi-axis manufacturing and processing of objects with nanometre precision…
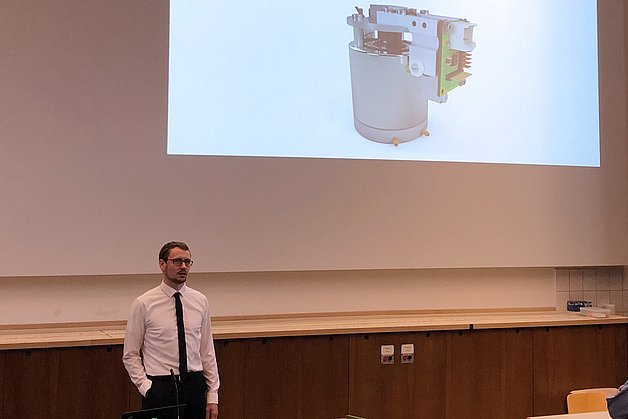
Press release,
Ready for Take-off – Vertikalantrieb für die 3D-Nanofertigung vorgestellt
IMMS-Doktorand verteidigt Promotion im DFG-Graduiertenkolleg NanoFab
You might also be interested in
Contact
Contact
Dipl.-Hdl. Dipl.-Des. Beate Hövelmans
Head of Corporate Communications
beate.hoevelmans(at)imms.de+49 (0) 3677 874 93 13
Beate Hövelmans is responsible for the text and image editorial work on this website, for the social media presence of IMMS on LinkedIn and YouTube, the annual reports, for press and media relations with regional and specialist media and other communication formats. She provides texts, photographs and video material for your reporting on IMMS, arranges contacts for interviews and is the contact person for events.