Project Ko²SiBus
Novel methods have been developed with which data lines in running industrial plant can be monitored cost-efficiently.
Until now no continuous monitoring of communication lines in interconnected machinery
The conditions and processes in machines and industrial plant are continuously monitored to enable highly automated processes in industry to run smoothly. However, what is still missing, because there has been no suitable procedure to do so, is the wiring of ethernet based communications which enables rapid, secure data exchange and links up networked industrial plant. It is only at the commissioning or during maintenance (if the machine is stopped for the purpose) that these physical connections are checked. But cables in production areas can be put under great strain by constant bending: for instance, when they are carried over drag chains. The strain can cause the data transfer quality to deteriorate and may even lead to cable breakages. With current methods, such changes in the cable properties are not at present being monitored, which makes the cables an additional weak point in any system.
A solution for continuously monitoring communication cables to ensure trouble-free production
With a view to reducing the associated downtime and maintenance effort to a minimum, methods were designed, developed and evaluated in the Ko2SiBus project, to enable the monitoring of the signal quality in the Ethernet cable continuously and cost-effectively for a plant during its regular operation without any interruption to the actual communications. The methods conceived were implemented in the form of a prototype. Its effectiveness was proven in laboratory tests.
This should not only make it easier to plan maintenance work. The new concept should also make it possible to pass on the data from the monitoring through a unified open interface so that it can be easily integrated into customer-specific control systems,possibly as a switch extension or as a feature installed directly into the end device.
IMMS created a circuit concept and constructed a demonstrator
The role of IMMS in the continuous monitoring scheme of communication lines was to design an embedded system and develop the appropriate circuit concepts, creating a system that tracks physical signal parameters using integrated analogue and digital components and reports any deviations to a monitoring centre. The functionality was tested with a demonstrator largely built by IMMS. The demonstrator maps the entire start-to-finish system from the signal measurements through to graphical representation of the analysis and the integration possibilities. It can also be used to manipulate the Ethernet signals very specifically, for example to simulate cable faults artificially or to show the influence of such faults.
Acronym / Name:
Ko²SiBus / Continuous and cost-effective signal monitoring for industrial bus systemsDuration:2017 – 2019
Application:
Automation technology and Industry 4.0|Industry 4.0 (I4.0)| Condition MonitoringResearch field:Smart distributed measurement and test systems
Related content
Reference
Friedrich Becker, TURCK Electronics GmbH
“With its experience in the spheres of signal processing and integrating communications and systems for industry, IMMS contributed significantly to the execution of the science which the partners in Chemnitz and Offenburg derived from theoretical principles in cable diagnostics and communications interfaces.”
Kontinuierliche Signalanalyse für Ethernet-Kabel
Sebastian Uziel1.elmug4future, Technologiekonferenz, 21. - 22. September 2021, ComCenter Brühl, Erfurt
1IMMS Institut für Mikroelektronik- und Mechatronik-Systeme gemeinnützige GmbH, Ehrenbergstraße 27, 98693 Ilmenau, Germany.Kontinuierliches Monitoring von Ethernet-Kabeln
Sebastian Uziel1.Online-Stammtisch Sensorik 4.0, Diagnoselösungen in der industriellen Anwendung, 20. Mai 2021, online
1IMMS Institut für Mikroelektronik- und Mechatronik-Systeme gemeinnützige GmbH, 98693 Ilmenau, Germany.Ko2SiBus - Kontinuierliche und Kostengünstige Signalanalyse für Ethernet-basierte Bus-Systeme
Sebastian Uziel1. Manuel Schappacher2.Fachzeitschrift Elektronik, 08.2020, 9. April 2020, S. 28 - 34
1IMMS Institut für Mikroelektronik- und Mechatronik-Systeme gemeinnützige GmbH, 98693 Ilmenau, Germany. 2FH Offenburg.A Cost-Efficient and Continuous Ethernet Cable Diagnosis Technique based on Undersampling
Ahmed Yahia Kallel1. Sebastian Uziel2. Manuel Schappacher3. Axel Sikora3. Thomas Keutel1. Olfa Kanoun1.2019 10th IEEE International Conference on Intelligent Data Acquisition and Advanced Computing Systems: Technology and Applications (IDAACS), Metz, France,18 - 21 September 2019, pp. 695-700. DOI: doi.org/10.1109/IDAACS.2019.8924458
1Technische Universität Chemnitz, Germany. 2IMMS Institut für Mikroelektronik- und Mechatronik-Systeme gemeinnützige GmbH, 98693 Ilmenau, Germany. 3Hochschule Offenburg, Germany.
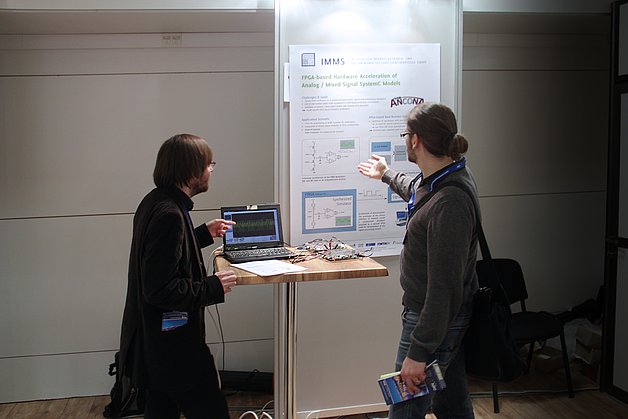
Event,
IDAACS 2019
Contribution to the 10th IEEE International Conference on Intelligent Data Acquisition and Advanced Computing Systems: Technology and Applications
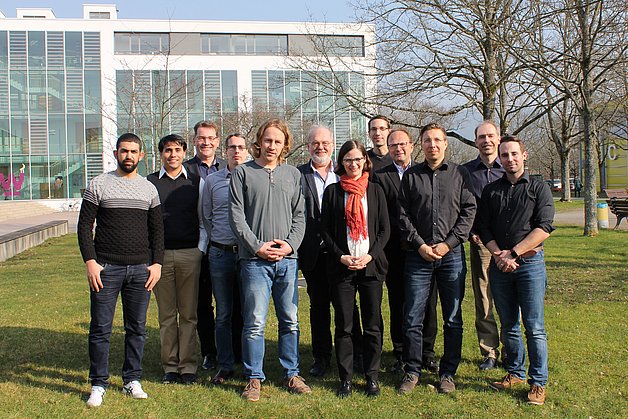
Press release,
Neue Methoden zum kostengünstigen Monitoring von Datenleitungen in laufenden Industrieanlagen
Forschungsvorhaben im Projekt Ko²SiBus zum Konsortialtreffen vor Industrievertretern vorgestellt
Contact
Contact
Dr.-Ing. Tino Hutschenreuther
Head of System Design
tino.hutschenreuther(at)imms.de+49 (0) 3677 874 93 40
Dr. Tino Hutschenreuther will answer your questions on our research in Smart distributed measurement and test systems and the related core topics Analysis of distributed IoT systems, Embedded AI and Real-time data processing and communications, on the lead applications Adaptive edge AI systems for industrial application and IoT systems for cooperative environmental monitoring as well as on the range of services for the development of embedded systems.
Funding
The Ko2SiBus project was funded by the DFAM (German Research Association for Automation and Microelectronics e.V.) via the AiF (German Federation of Industrial Research Associations) as IGF project by the Federal Ministry of Economics and Energy under the reference 19574 BG by a resolution of the German Bundestag.